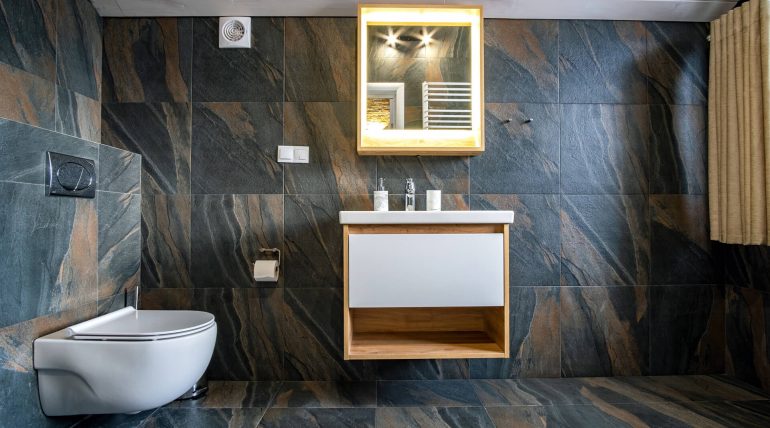
How to Prepare Your Surface for a Flawless Tile Installation
Think of tile installation like building a house. Without a strong and stable foundation, the entire structure is compromised. In the world of tiling, that foundation is the substrate – the surface you’ll be tiling over. Skipping or skimping on surface preparation is one of the most common and detrimental mistakes in tile installation. A flawless tile job starts long before you mix your thin-set. This comprehensive guide will walk you through the essential steps of preparing various surfaces for a successful and long-lasting tile installation, ensuring your finished project is as durable as it is beautiful.
Why Surface Preparation is Non-Negotiable
Surface preparation is not just a suggestion; it’s a fundamental requirement for a durable tile installation. The thin-set mortar that bonds the tile to the substrate relies on a clean, stable, and properly prepared surface for optimal adhesion and performance. Neglecting this crucial step can lead to a host of problems down the line, including:
- Poor Adhesion: Thin-set won’t properly bond to dirty, dusty, or unstable surfaces, leading to loose or “hollow” tiles.
- Cracking: Movement in the substrate due to unevenness or structural issues can cause the tiles or grout to crack.
- Lippage: Uneven surfaces result in lippage, where the edges of adjacent tiles are not level, creating a tripping hazard and an aesthetically displeasing finish.
- Water Damage: Cracks in the grout or tile, often caused by substrate issues, can allow water to penetrate and damage the underlying structure, leading to mold, mildew, and rot.
- Premature Failure: All of these issues ultimately contribute to the premature failure of the entire tile installation, requiring costly repairs or replacement.
According to a survey conducted by a leading tile industry publication in 2021, improper surface preparation was cited as a contributing factor in over 60% of tile installation failures reported by contractors.
Assessing Your Substrate: The First Step
Before you begin any preparation work, you need to assess the existing substrate. Different materials require different preparation methods. Common substrates for tiling include:
- Concrete
- Wood (plywood or OSB)
- Drywall (for walls)
- Existing Tile
- Cement Backer Board
Each of these materials has specific requirements for a successful tile installation. You also need to consider the condition of the substrate. Is it cracked? Is it uneven? Is there any existing damage or moisture?
General Surface Preparation Steps (Applies to Most Substrates)
While specific preparation varies by substrate, several general steps are crucial for almost any tiling project:
Step 1: Cleanliness is Key
The surface must be meticulously clean and free of any contaminants. This includes:
- Dirt and Dust: Sweep or vacuum the area thoroughly.
- Grease and Oil: Use a degreaser to remove any oily residue.
- Old Adhesives or Grout: Scrape away any remnants of old tile adhesive, grout, or flooring materials.
- Paint or Sealers: Remove any peeling paint or sealers that could prevent the thin-set from bonding.
Example: Trying to tile over a greasy kitchen floor will likely result in the thin-set not adhering properly, leading to tiles popping up over time. A simple cleaning with a degreaser can prevent this costly issue.
Step 2: Ensure the Surface is Dry
Moisture is the enemy of tile installation. The substrate must be completely dry before you begin. Excessive moisture can lead to poor adhesion, mold growth, and even structural damage.
- Check for Moisture: Use a moisture meter to check the moisture levels of the substrate, especially concrete slabs.
- Address Any Leaks: Identify and repair any sources of moisture or leaks before proceeding.
- Allow Adequate Drying Time: Give the surface sufficient time to dry after cleaning or any repairs involving water.
Statistic: According to the National Tile Contractors Association (NTCA), moisture-related issues are a significant factor in a substantial percentage of tile installation failures, highlighting the importance of proper drying and, in some cases, moisture mitigation.
Step 3: Leveling and Flattening the Substrate
A flat and level surface is essential for a smooth and professional-looking tile installation. Unevenness in the substrate will transfer through the thin-set and result in lippage between the tiles.
- Check for Levelness: Use a long level or a straightedge to check for high and low spots on the surface.
- Fill Low Spots: Use a patching compound or self-leveling underlayment to fill in low areas. Follow the product manufacturer’s instructions for mixing and application.
- Grind High Spots: Use a grinder to level out any high spots.
Case Study: A DIYer skipped leveling a slightly uneven concrete floor before tiling. The resulting floor had noticeable lippage, making it uncomfortable to walk on and difficult to clean. Fixing the issue required removing the new tile and starting over after properly leveling the floor.
Step 4: Structural Soundness
The substrate must be structurally sound and able to support the weight of the tile and the expected load. This is particularly important for wood subfloors.
- Inspect for Damage: Check for any signs of rot, water damage, or excessive flexing.
- Reinforce if Necessary: For wood subfloors, ensure the joists are adequately spaced and consider adding an additional layer of plywood (typically exterior grade) for added rigidity. The thickness of the subfloor is critical for preventing movement. Consult industry standards for recommended subfloor thicknesses based on joist spacing and tile type.
- Address Cracks in Concrete: Repair any significant cracks in concrete slabs using an epoxy crack filler or other appropriate repair material.
Specific Substrate Preparation
Here’s a look at the specific preparation required for common substrates:
Concrete Subfloors
- Cleaning and Leveling: Follow the general steps above.
- Moisture Testing: Essential for concrete. Conduct a moisture test (e.g., calcium chloride test or relative humidity test) to ensure the slab is sufficiently dry for tiling.
- Addressing Cracks: Repair non-moving cracks. For moving cracks or control joints, consider incorporating a crack isolation membrane.
- Sealing (if necessary): Some concrete surfaces may require sealing or priming depending on their porosity and condition.
Wood Subfloors (Plywood or OSB)
- Ensure Rigidity: The subfloor must be stiff enough to prevent flexing, which can cause the tile and grout to crack. Consult industry standards (like the TCNA Handbook) for minimum subfloor thicknesses and joist spacing requirements.
- Add Underlayment: Typically, a layer of cement backer board or a similar approved underlayment is installed over the wood subfloor to provide a stable and dimensionally stable surface for tiling.
- Fasten Securely: Ensure the underlayment is properly fastened to the subfloor using recommended screws or nails.
- Seal Edges (if necessary): For some types of underlayment, sealing the edges may be required.
Drywall (for Walls)
- Ensure it’s Water-Resistant: In wet areas like showers or behind sinks, use water-resistant drywall (greenboard) or, preferably, cement backer board or a liquid waterproofing membrane applied directly to the drywall. Standard drywall is not suitable for wet areas.
- Repair and Smooth: Patch any holes or imperfections and ensure the surface is smooth.
- Prime: Apply a suitable primer to the drywall to promote adhesion of the thin-set.
Existing Tile
Tiling over existing tile is possible in some cases, but it requires careful assessment.
- Assess Condition: Ensure the existing tile is well-adhered, clean, and free of cracks or damage.
- Clean Thoroughly: Clean the existing tile and grout lines meticulously to remove all soap scum, grease, and grime.
- Roughen the Surface: Lightly sand or grind the surface of the existing tile to create a प्रोफाइल for the new thin-set to adhere to.
- Use the Right Thin-set: Use a thin-set specifically designed for tiling over existing tile.
- Consider the Added Height: Tiling over existing tile will raise the floor level, which may impact transitions to adjacent rooms or the clearance of doors.
Cement Backer Board
Cement backer board is a popular and excellent substrate for tiling, especially in wet areas.
- Proper Installation: Ensure the backer board is properly installed according to the manufacturer’s instructions, including screw spacing and joint treatment (taping and mudding the joints with thin-set).
- Waterproofing (if necessary): While backer board is water-resistant, it is not waterproof. In wet areas like showers, a liquid waterproofing membrane or a sheet membrane should be applied over the backer board.
The Importance of Waterproofing in Wet Areas
In bathrooms, showers, and other areas prone to moisture, proper waterproofing is non-negotiable. Water seeping behind the tiles can lead to serious and costly damage to the structure of your home.
- Types of Waterproofing: Common waterproofing methods include liquid applied membranes and sheet membranes.
- Coverage: Ensure the waterproofing is applied correctly and covers all necessary areas, including corners, seams, and around drains and fixtures.
According to the National Association of Home Builders (NAHB), water intrusion is a leading cause of construction defect claims, and proper waterproofing in wet areas is a critical preventative measure.
Conclusion
Surface preparation is the unsung hero of a successful tile installation. While it might seem like a tedious step, investing the time and effort to properly prepare your substrate will pay dividends in the form of a durable, beautiful, and long-lasting tiled surface. By thoroughly cleaning, ensuring dryness, leveling, addressing structural issues, and implementing appropriate waterproofing where needed, you create the ideal foundation for your tiles to thrive. Don’t underestimate the power of preparation – it’s the key to unlocking a truly flawless tile installation.